Important Reasons For Regular Silo Servicing
Why Do Silos Need Servicing?
As well as regular maintenance, your silo should be designed to withstand the elements and to increase longevity. Preventative maintenance is just as important as scheduled servicing - maybe more so.
Many things can lead to silo damage, including improper filling and unloading of the silo, and weak foundations. These issues can go unnoticed if your silo isn’t regularly serviced, which is why you should get your silo serviced at least once a year.
Proper care and inspection of your silo will increase the life of the silo as well and reduce the need for repairs.
To Protect Your Materials
Some silos are made using large steel sheets that have ribbing on the inside, which helps to reduce the build-up of product on the sides of the silo. However, this doesn’t mean that there won’t be any build-up.
After some time bulk materials will build up and become compacted on the sides of the silo, which will need to be knocked off during servicing. This clumping can cause blockages and means less material will in the emptying process, so you’ll be losing material.
It also lowers the predictability of your offloading process and causes off-centre loading, which can change the amount of pressure on the walls and damage your equipment.
This can all be avoided by getting your silo regularly serviced and keeping a close eye on each step of the loading and offloading process.
To Identify Issues
Regular maintenance will pick up on issues such as wear, blockages, and structural failures. It’s a way to pick up on minor issues before they develop into more costly or dangerous problems.
Even if durable materials are used in the silo design, weather and time can still cause wear on the silo body. Degradation can show differently depending on the silo’s construction and the bulk materials stored in it.
Concrete silos may exhibit cracks and crumble, whereas steel silo issues can include the build-up of material and corrosion.
Once inspections have been completed, you’ll receive results and maintenance will be performed - which is a lot better than waiting for something to break and having to break the bank fixing a whole system collapse.
Thankfully, most silo failures don’t occur suddenly - your silo will exhibit signs of distress and you’ll pick up on these problems and get them serviced. It’s important to catch potential failures early so they can be quickly addressed with minimal damage.
For Safety Reasons
Silos can be as tall as 90m and as wide as 90ft and can store tonnes of bulk material, so if there are any structural failures, lives could be at risk.
Regular maintenance can pick up on any potential structural failures, as well as corrosion and accidental damage. Every silo, whether it be made of steel, fibreglass, or concrete, has a support structure that will need to be regularly inspected as a safety precaution.
Although there have been no reported fatalities in the UK from a silo failure, that doesn’t mean that it can't happen. In Europe, there have been cases of loss of life from silo failure, which could have been prevented with regularly scheduled silo maintenance.
What Needs To Be Serviced?
Your silo should be serviced once a year at least, but professional inspections can be as little as every 5 years - although it’s not recommended.
Some things that need to be inspected closely include:
Roofs
Roofs are one of the main parts of the silo and work with the silo body to keep the bulk materials dry and protected. If there are any problems with the roof, leaking can occur which may lead to contamination, lowering the quality of your product.
Any roof leaks can lead to corrosion on the inside of the silo, as well as the roof beams - which can cause structural damage.
Flaking on the roof beam pockets can expose the beams and cause the roof to collapse, which is something that can be avoided by checking this regularly.
Silo Exterior
During in-house or professional inspections, exterior surfaces are always something you should inspect closely. Look for any cracks on the walls, roofs, and foundations as this is an indicator of stress.
It’s important to catch these things early before they develop into holes or total wall failure and collapse - which would be a lot more expensive and damaging than a regular checkup.
You should also look out for any signs of corrosion and rust, as this can lead to silo failure if left untreated.
Silo Cone
The cone construction and design can hugely affect the performance, and if best practices and safety precautions are not adhered to, silo cone failure can become a costly problem.
The silo cone inspections should be left to professionals as safety practices need to be followed.
Silo cone failure can be easily prevented by routine silo servicing. However, silo cone inspections should be left to professionals as safety practices need to be followed.
The inspector will look for ways that the silo can be improved, as well as the materials used and the thickness of the silo wall.
Suspended cones are no longer best practice, as this type of silo, unfortunately, has a high failure rate, and will need more repairs than the new standard. The inspector will recommend that you update this, and it should be addressed during servicing.
Bulk Material Buildup
The buildup of material is likely to occur if the silo hasn’t been cleaned in a while, or if the interior doesn’t feature ribbing.
The buildup can lead to clumping, which can cause a skewed flow and unbalanced pressure, potentially damaging any equipment and losing material.
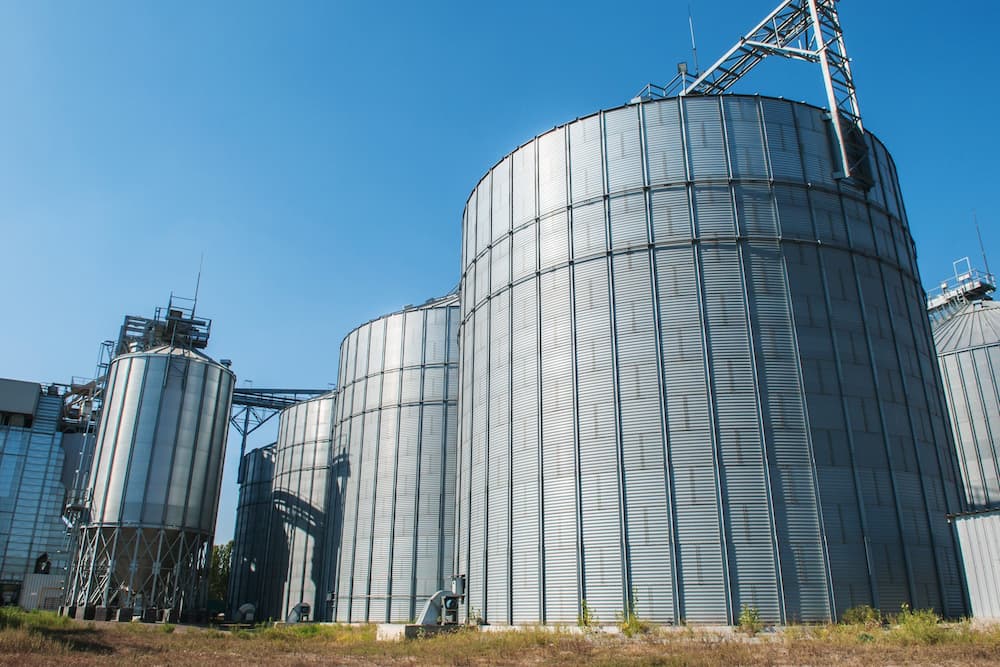
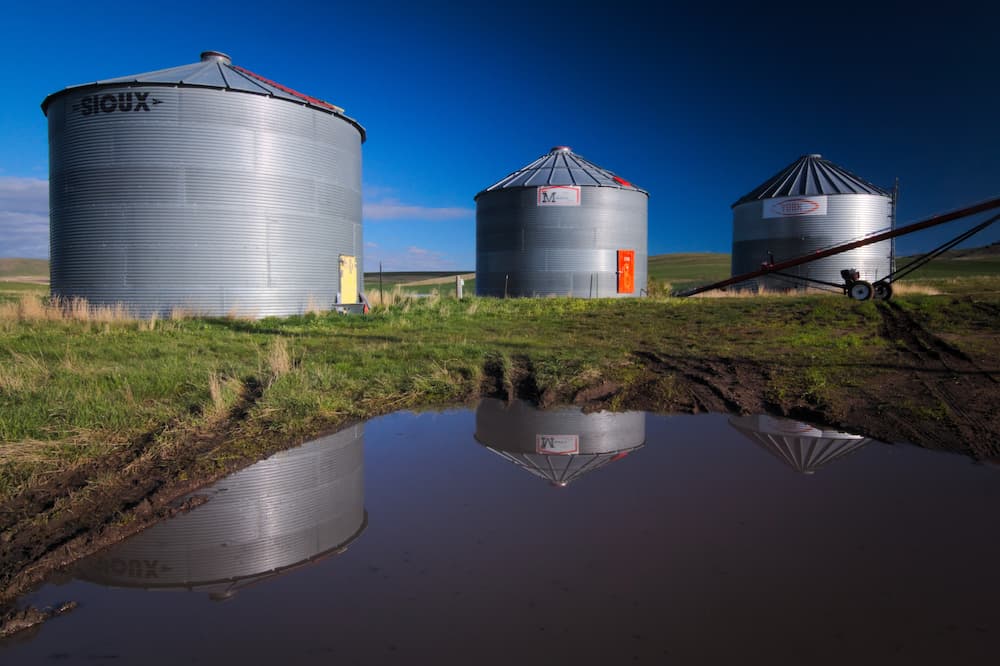
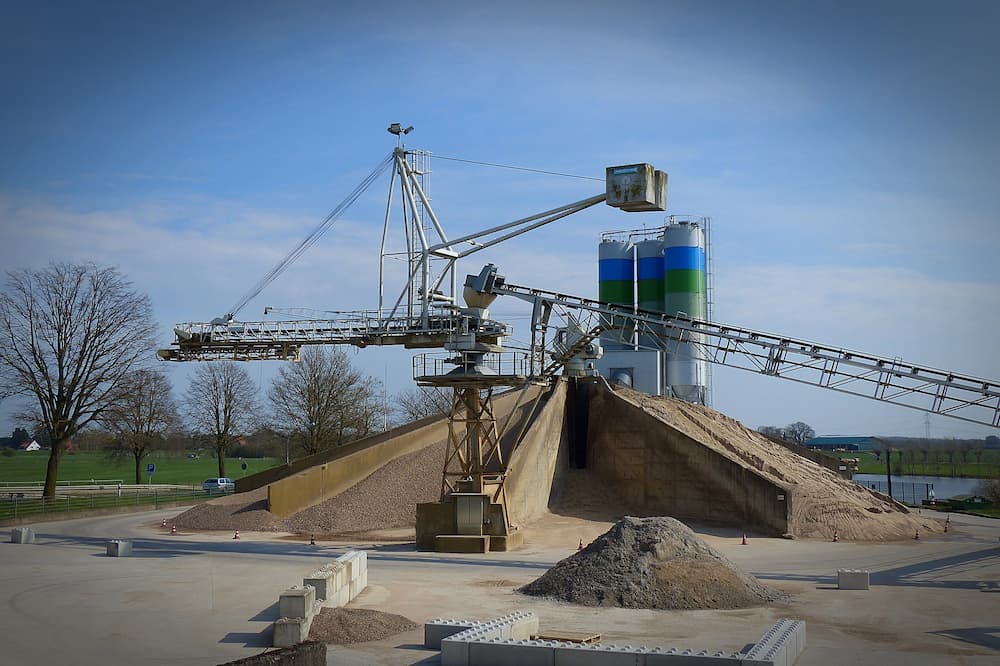